News / National
Zimbabwe industry cuts working hours
26 Oct 2017 at 13:51hrs | Views
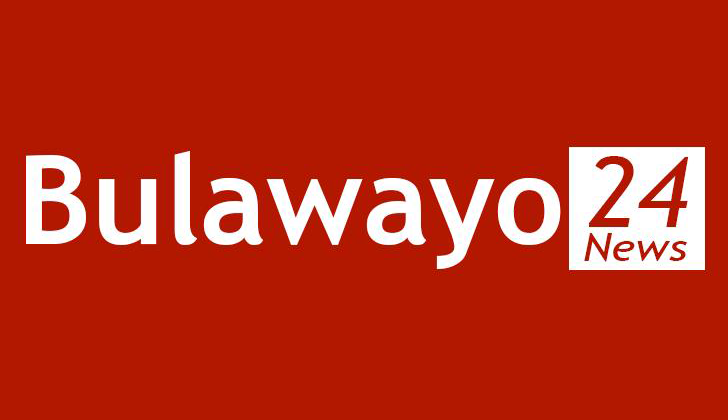
Zimbabwe's manufacturers have been squeezed harder by the deteriorating economy, with the sector retrenching and cutting working hours on the back of decreased capacity utilisation, the latest Confederation of Zimbabwe Industries (CZI)'s survey has revealed.
This comes as the struggling companies' woes have recently been escalated by the deepening foreign currency crisis, which has forced them to turn to the illegal parallel market where dealers are charging punitively steep premiums.
According to the CZI 2017 Manufacturing Survey released yesterday, most of the companies retrenched due to waning business on the back of subdued economic activity, characterised by the erosion of disposable incomes and a slump in aggregate demand.
"The total employment in the manufacturing sector declined by an average 15,2 percent in 2017," CZI said in the survey.
"The majority of respondents (74 percent) who retrenched indicated that it was due to the decline in business as a result of low orders," the Confederation said, adding "they also cited operational challenges and the need to cut labour costs, which in themselves are high".
Others, CZI said, laid off workers as part of right-sizing and remodelling business operations.
It said "the proportion of permanent employees vis-à-vis non-permanent . . . is close to one as to one".
CZI noted that majority of the companies were forced to cut working hours, particularly for employees directly involved in the production process, in response subdued operating environment.
"On a discouraging note, . . . 77 percent expressed that they changed working hours for negative reasons (which include) reduction in workload and output, drop in aggregate demand, to reduce labour costs, inability to pay (wages) and other related utilities," the Confederation said.
Only 23 percent of the companies changed working hours because of increase in production.
While manufactured output volume grew 5,5 percent, the sector's capacity utilisation dropped 2,3 percent from 47,4 percent in 2016 to 45,1 percent this year.
"The drop has been driven by sectors such as non-metallic mineral products, wood and furniture, transport and equipment production and petroleum products," CZI said.
Highlighting the importance of retooling, the confederation said the "output growth was recorded by companies whose machinery is less than ten years old".
"Companies with older machinery and equipment did not record any growth . . .," it said.
However, Reserve Bank of Zimbabwe governor John Mangudya questioned the approach used in the survey to measure industry activity.
"Should we measure capacity utilisation or growth? Is that approach relevant to what we want to achieve?" he queried.
He argued that the focus must be on growth not capacity utilisation.
"We have excess investment in capacity in Zimbabwe," he highlighted, giving the oil expressers industry as an example.
The central bank chief said the country had seven major oil expressers — under the Oil Expressers Association of Zimbabwe — that produced about 45 million litres of cooking per month, yet national consumption is only 10 million litres monthly.
"There are producing excess of 35 million litres, which could be exported. You would realise that two of the seven expressers can produce enough for the country."
Commenting on the research's findings, CZI chief economist Dephine Mazambani said the major challenges contributing to the manufacturing sector's demise was failure to retool, which has forced companies to use antiquated and inefficient machinery — 89 percent more than two decades old, limited access to affordable capital, corruption and the foreign currency crisis, which has of late deepened.
She said the escalating foreign currency crisis had dealt a major blow to the sector.
"50 percent companies have had their expenses increase because of the additional costs incurred in accessing foreign currency," Mazambani said.
Due to the monetary authorities' failure to allocate enough foreign currency, companies have reportedly turned to the parallel market where they pay exorbitant premiums to secure the scarce greenback.
Crucially, she said optimism was low among most manufacturers.
"More than 50 percent of the manufacturing sector players are pessimistic of the economic outlook," she said, adding that the firms feel "fundamentals remain unaddressed".
In the survey, CZI said "notwithstanding the positive developments . . . we see deterioration in business confidence".
"Companies are failing to access raw materials as a result of the foreign exchange shortage . . . When business cannot control its access to foreign exchange, planning becomes impossible," it said, adding that the challenges are exacerbated by the "increase in inflationary pressures".
CZI said the pervasive lack of confidence in the economy was "hurting new investment".
Former CZI president Joseph Kanyekanye weighed in: "We are far from having an exporting industry. We are far from having an industry that is not reliant on foreign currency."
This comes as the struggling companies' woes have recently been escalated by the deepening foreign currency crisis, which has forced them to turn to the illegal parallel market where dealers are charging punitively steep premiums.
According to the CZI 2017 Manufacturing Survey released yesterday, most of the companies retrenched due to waning business on the back of subdued economic activity, characterised by the erosion of disposable incomes and a slump in aggregate demand.
"The total employment in the manufacturing sector declined by an average 15,2 percent in 2017," CZI said in the survey.
"The majority of respondents (74 percent) who retrenched indicated that it was due to the decline in business as a result of low orders," the Confederation said, adding "they also cited operational challenges and the need to cut labour costs, which in themselves are high".
Others, CZI said, laid off workers as part of right-sizing and remodelling business operations.
It said "the proportion of permanent employees vis-à-vis non-permanent . . . is close to one as to one".
CZI noted that majority of the companies were forced to cut working hours, particularly for employees directly involved in the production process, in response subdued operating environment.
"On a discouraging note, . . . 77 percent expressed that they changed working hours for negative reasons (which include) reduction in workload and output, drop in aggregate demand, to reduce labour costs, inability to pay (wages) and other related utilities," the Confederation said.
Only 23 percent of the companies changed working hours because of increase in production.
While manufactured output volume grew 5,5 percent, the sector's capacity utilisation dropped 2,3 percent from 47,4 percent in 2016 to 45,1 percent this year.
"The drop has been driven by sectors such as non-metallic mineral products, wood and furniture, transport and equipment production and petroleum products," CZI said.
Highlighting the importance of retooling, the confederation said the "output growth was recorded by companies whose machinery is less than ten years old".
"Companies with older machinery and equipment did not record any growth . . .," it said.
However, Reserve Bank of Zimbabwe governor John Mangudya questioned the approach used in the survey to measure industry activity.
He argued that the focus must be on growth not capacity utilisation.
"We have excess investment in capacity in Zimbabwe," he highlighted, giving the oil expressers industry as an example.
The central bank chief said the country had seven major oil expressers — under the Oil Expressers Association of Zimbabwe — that produced about 45 million litres of cooking per month, yet national consumption is only 10 million litres monthly.
"There are producing excess of 35 million litres, which could be exported. You would realise that two of the seven expressers can produce enough for the country."
Commenting on the research's findings, CZI chief economist Dephine Mazambani said the major challenges contributing to the manufacturing sector's demise was failure to retool, which has forced companies to use antiquated and inefficient machinery — 89 percent more than two decades old, limited access to affordable capital, corruption and the foreign currency crisis, which has of late deepened.
She said the escalating foreign currency crisis had dealt a major blow to the sector.
"50 percent companies have had their expenses increase because of the additional costs incurred in accessing foreign currency," Mazambani said.
Due to the monetary authorities' failure to allocate enough foreign currency, companies have reportedly turned to the parallel market where they pay exorbitant premiums to secure the scarce greenback.
Crucially, she said optimism was low among most manufacturers.
"More than 50 percent of the manufacturing sector players are pessimistic of the economic outlook," she said, adding that the firms feel "fundamentals remain unaddressed".
In the survey, CZI said "notwithstanding the positive developments . . . we see deterioration in business confidence".
"Companies are failing to access raw materials as a result of the foreign exchange shortage . . . When business cannot control its access to foreign exchange, planning becomes impossible," it said, adding that the challenges are exacerbated by the "increase in inflationary pressures".
CZI said the pervasive lack of confidence in the economy was "hurting new investment".
Former CZI president Joseph Kanyekanye weighed in: "We are far from having an exporting industry. We are far from having an industry that is not reliant on foreign currency."
Source - dailynews