News / National
Tax scam costs Govt billions
10 Jul 2019 at 07:34hrs | Views
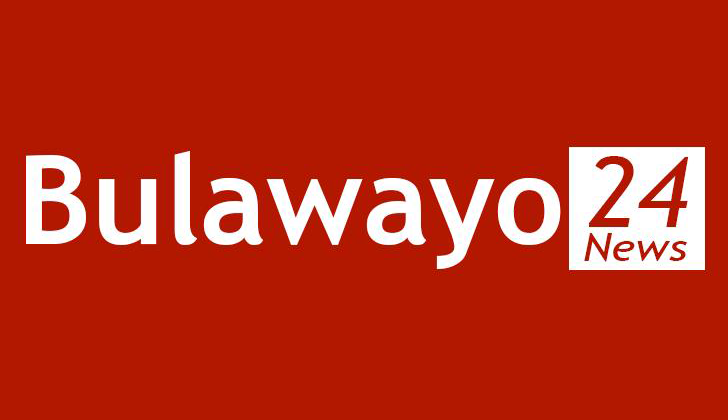
Some players in the garment-making sector are allegedly skimming the Government of billions of dollars in potential tax revenue and suffocating downstream textile industries by abusing a special clothing manufacturers' rebate (CMR) designed to protect domestic apparel producers from external competition.
A month-long investigation into the conduct of some industry players showed that after benefiting from the rebate on imported fabrics, some clothing manufacturers were using transfer pricing, under-invoicing and incorrect declarations to evade local taxes while taking advantage of preferential trade agreements to realise huge profits in regional markets.
This comes at a time when the Government has adopted zero tolerance to corruption, arrested and started prosecuting high-profile people. It also comes at a time when Government has created a special anti-corruption unit in the president's office and reconstituted the Zimbabwe Anti-Corruption Commission (ZACC).
Documents seen by The Herald show that in one glaring case, one of the country's major garment manufacturing companies (name withheld) with factories in Southerton, Harare and Belmont, Bulawayo, made work suits at an average cost of $9 per unit which were surprisingly exported to South Africa for a paltry $6.
Further investigations revealed that the "exported" work suits had simply been moved to a sister company in South Africa which later sold each unit for R250 (about $150 at the official interbank exchange rate) after being accompanied by Sadc and Comesa certificates which exempted the Zimbabwean entity from paying duties for exports into the South African market.
With the National Employment Council (NEC) for Clothing Industry agreeing to pay a minimum monthly wage of $237 beginning April this year compared to the R3 500 ($2,124) awarded to South African workers in January, the company realised super profits after benefiting from the very cheap local labour and duty exemptions in Zimbabwe and South Africa.
So low were the local wages that the company was able to pay a monthly salary for a Grade A tailor and remain with $50 change after selling only two work suits in South Africa.
"While there is absolutely nothing wrong with local companies exporting goods and making huge profits, it becomes worrying when the companies deny the Government its dues by evading tax.
"When a company purports to export a product at a price below the manufacturing cost, something doesn't add up and suspicion must be raised.
"The Government needs to investigate who the companies are exporting to, because it has become clear that some of them are engaging in transfer pricing and exporting to their companies domiciled in other countries," said a source close to the investigation.
"What is unfortunate is that some of the companies benefitting from statutory instruments are constantly hiking prices and compromising the popularity of the very Government that sought to bail them out."
Over 50 companies are enjoying protection under Statutory Instrument 32 of 2015 cited as Customs and Excise (Clothing Manufacturer) Rebate Regulations.
The clothing manufacturers' rebate (CMR) was introduced after stakeholders lobbied the Ministry of Finance and the Ministry of Industry and Commerce to prop up the struggling industry and allows apparel makers to import fabrics from man-made yarn, duty free.
Materials eligible for the rebate include denim, cotton sewing thread, woven fabrics of polyester staple fibres, chenille fabrics, tulles and other net fabrics.
The fabrics are kept in bonded warehouses from where they are withdrawn under the supervision of the Zimbabwe Revenue Authority (Zimra) as and when they are required for use. However, 100 percent cotton fabrics are not covered under this rebate as they are produced locally.
Indications are that some players in the industry have been importing material that is locally available and later producing garments for the international market, a development that is threatening to destroy downstream players such as cotton farmers, ginners, spinners and weavers. Some of the locally produced fabrics that are being imported include cloths for protective clothing and T-shirts.
Three years ago Zimspin, a local producer of fabric, had plenty of stocks but ended up selling the material at a loss for $1 instead of $2,95 owing to a glut of cheap imports.
An industry analyst said the country had over the years continued watching huge textile companies such as David Whitehead and Cone Textiles going under because of serious viability challenges adding that there was need for a relook into policies governing the industry. It was out of greed that some players in the clothing industry were continuing to push for the extension of the rebate instead of working hard to help the local textile industry overcome the challenge of cheap imported fabric.
Zimbabwe Textile Manufacturer's Association (ZTMA) president Mr Admire Masenda said they were not aware of any companies abusing the CMR but said authorities should come down hard on anyone breaching laws and regulations.
"By introducing the CMR, the intention of the Government was to help local clothing manufacturers to be competitive in the region. We have not received reports on anyone abusing the rebate but it is possible for some to be involved in such things as under-invoicing and false declarations," said Mr Masenda.
He said imported fabrics such as polyester and poly cotton were cheaper than 100 percent cotton enabling local garment makers to make cheaper and competitive products for the export market. Zimbabwe Clothing Manufacturers association chairman Mr Jeremy Youmans said it was possible for some companies to abuse the CMR by selling imported fabrics on the local market instead of making them into garments.
"I am not aware of any malpractices but if there is anyone abusing the CMR, we will certainly report them to Zimra," said Mr Youmans. Cotton Company of Zimbabwe managing director Mr Pious Manamike said the government needed to tighten controls to ensure that there was no abuse of any facilities by industry players.
Asked whether it would be prudent for the government to review the CMR in the wake of its alleged abuse Mr Manamike said: "For now the textile industry is not yet fully functional. We have to get the industry up and running before we start talking about restricting imports.
"This can create shortages and we move from one problem to another. What the authorities would rather do is to deal with specific companies found to be in breach of laws. Another industry player Mr Kingston Mhako, whose company Kingsport specialises in corporate wear and custom made apparel, opined that the government could remove the statutory instrument in question to ensure that importers paid the right duties and then give incentives to exporters upon presentation of the necessary documents showing that all transactions were above board.
"We can have a situation where exporters apply for a duty drawback from Zimra who will then refund any duties after being satisfied that imported materials were subsequently exported,' said Mr Mhako.
Duty drawback is the refund, reduction or waiver in whole or in part of customs duties assessed or collected upon importation of an article or materials which are later exported. James Doward of Glendale Spinners declined to comment on the issue.
A month-long investigation into the conduct of some industry players showed that after benefiting from the rebate on imported fabrics, some clothing manufacturers were using transfer pricing, under-invoicing and incorrect declarations to evade local taxes while taking advantage of preferential trade agreements to realise huge profits in regional markets.
This comes at a time when the Government has adopted zero tolerance to corruption, arrested and started prosecuting high-profile people. It also comes at a time when Government has created a special anti-corruption unit in the president's office and reconstituted the Zimbabwe Anti-Corruption Commission (ZACC).
Documents seen by The Herald show that in one glaring case, one of the country's major garment manufacturing companies (name withheld) with factories in Southerton, Harare and Belmont, Bulawayo, made work suits at an average cost of $9 per unit which were surprisingly exported to South Africa for a paltry $6.
Further investigations revealed that the "exported" work suits had simply been moved to a sister company in South Africa which later sold each unit for R250 (about $150 at the official interbank exchange rate) after being accompanied by Sadc and Comesa certificates which exempted the Zimbabwean entity from paying duties for exports into the South African market.
With the National Employment Council (NEC) for Clothing Industry agreeing to pay a minimum monthly wage of $237 beginning April this year compared to the R3 500 ($2,124) awarded to South African workers in January, the company realised super profits after benefiting from the very cheap local labour and duty exemptions in Zimbabwe and South Africa.
So low were the local wages that the company was able to pay a monthly salary for a Grade A tailor and remain with $50 change after selling only two work suits in South Africa.
"While there is absolutely nothing wrong with local companies exporting goods and making huge profits, it becomes worrying when the companies deny the Government its dues by evading tax.
"When a company purports to export a product at a price below the manufacturing cost, something doesn't add up and suspicion must be raised.
"The Government needs to investigate who the companies are exporting to, because it has become clear that some of them are engaging in transfer pricing and exporting to their companies domiciled in other countries," said a source close to the investigation.
"What is unfortunate is that some of the companies benefitting from statutory instruments are constantly hiking prices and compromising the popularity of the very Government that sought to bail them out."
Over 50 companies are enjoying protection under Statutory Instrument 32 of 2015 cited as Customs and Excise (Clothing Manufacturer) Rebate Regulations.
The clothing manufacturers' rebate (CMR) was introduced after stakeholders lobbied the Ministry of Finance and the Ministry of Industry and Commerce to prop up the struggling industry and allows apparel makers to import fabrics from man-made yarn, duty free.
The fabrics are kept in bonded warehouses from where they are withdrawn under the supervision of the Zimbabwe Revenue Authority (Zimra) as and when they are required for use. However, 100 percent cotton fabrics are not covered under this rebate as they are produced locally.
Indications are that some players in the industry have been importing material that is locally available and later producing garments for the international market, a development that is threatening to destroy downstream players such as cotton farmers, ginners, spinners and weavers. Some of the locally produced fabrics that are being imported include cloths for protective clothing and T-shirts.
Three years ago Zimspin, a local producer of fabric, had plenty of stocks but ended up selling the material at a loss for $1 instead of $2,95 owing to a glut of cheap imports.
An industry analyst said the country had over the years continued watching huge textile companies such as David Whitehead and Cone Textiles going under because of serious viability challenges adding that there was need for a relook into policies governing the industry. It was out of greed that some players in the clothing industry were continuing to push for the extension of the rebate instead of working hard to help the local textile industry overcome the challenge of cheap imported fabric.
Zimbabwe Textile Manufacturer's Association (ZTMA) president Mr Admire Masenda said they were not aware of any companies abusing the CMR but said authorities should come down hard on anyone breaching laws and regulations.
"By introducing the CMR, the intention of the Government was to help local clothing manufacturers to be competitive in the region. We have not received reports on anyone abusing the rebate but it is possible for some to be involved in such things as under-invoicing and false declarations," said Mr Masenda.
He said imported fabrics such as polyester and poly cotton were cheaper than 100 percent cotton enabling local garment makers to make cheaper and competitive products for the export market. Zimbabwe Clothing Manufacturers association chairman Mr Jeremy Youmans said it was possible for some companies to abuse the CMR by selling imported fabrics on the local market instead of making them into garments.
"I am not aware of any malpractices but if there is anyone abusing the CMR, we will certainly report them to Zimra," said Mr Youmans. Cotton Company of Zimbabwe managing director Mr Pious Manamike said the government needed to tighten controls to ensure that there was no abuse of any facilities by industry players.
Asked whether it would be prudent for the government to review the CMR in the wake of its alleged abuse Mr Manamike said: "For now the textile industry is not yet fully functional. We have to get the industry up and running before we start talking about restricting imports.
"This can create shortages and we move from one problem to another. What the authorities would rather do is to deal with specific companies found to be in breach of laws. Another industry player Mr Kingston Mhako, whose company Kingsport specialises in corporate wear and custom made apparel, opined that the government could remove the statutory instrument in question to ensure that importers paid the right duties and then give incentives to exporters upon presentation of the necessary documents showing that all transactions were above board.
"We can have a situation where exporters apply for a duty drawback from Zimra who will then refund any duties after being satisfied that imported materials were subsequently exported,' said Mr Mhako.
Duty drawback is the refund, reduction or waiver in whole or in part of customs duties assessed or collected upon importation of an article or materials which are later exported. James Doward of Glendale Spinners declined to comment on the issue.
Source - the herald