Business / Companies
Amplats investigates Unki Platinum Mine
22 Sep 2013 at 05:37hrs | Views
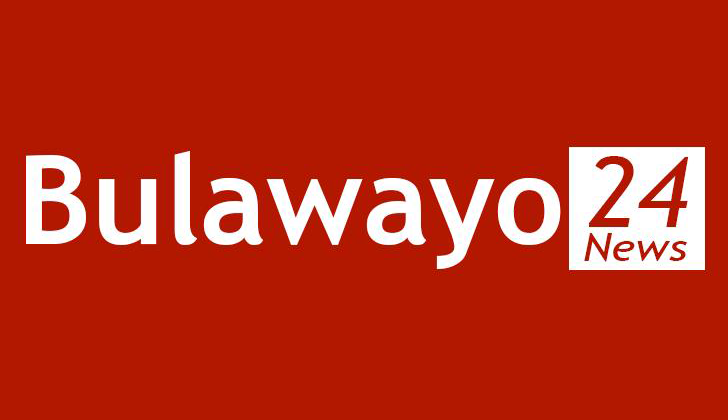
South African-based producer of platinum group metals Anglo American Platinum (Amplats) has launched an investigation into its wholly owned local subsidiary Unki Platinum Mine over a multi-million-dollar housing project that has gone sour after allegations of "exploitative contracts" that were given to Zimbabwean contractors, it has emerged.
In addition, the investigations extend to a "suspicious" deal between the miner's agent and a company roped in to supply materials.
Unki management has since confirmed the probe.
It is believed that the Johannesburg Stock Exchange-listed concern is worried that there might be a serious breach in the way the contracts with local contractors were negotiated, a development that might ultimately dent the construction project and inflate the aggregate cost of the venture.
Investigations by this paper show that on October 9 last year Unki Platinum Mine, which is based in Shurugwi, invited companies to tender for the construction of about 800 housing units valued at more than US$66 million.
Six contractors - Dohne, Citizen, Bambanani JV, Newbase Construction, Ubuntu JV and Selbridge - were subsequently awarded tenders.
The tenders were submitted for a supply-and-fix contract where contractors would be entitled to mark-ups on labour, plant and material costs.
Also, contracts entered into were in the form of the NEC3 contract, which is deliberately written to formalise the requirement to carry out good practice project management systems that should assist the project teams in understanding the status of both time and cost for the life cycle of the project.
However, in January this year the employer's agent, Amplats senior projects manager Mr Christian Muvingi, who is based in South Africa, introduced the materials aggregator model where virtually all the materials were going to be supplied by one company - Weldmax - that is also owned by a South African-based businessman, Mr Solomon Matsa.
Sources say the deal clinched by Weldmax, worth over US$26 million, raised eyebrows, particularly the unclear circumstances in which the company landed the award, and the rationale by the project manager to engage one supplier to source all the materials where six local contractors had been engaged.
But what has become more worrying for the stakeholders, including the contractors is the fact that the basic materials that have been supplied thus far, such as bricks, cement and termite poison, could not be supplied timely, while "some of the few materials supplied could not conform to the quality specifications captured in the contract".
And it is further alleged that when contractors tried to engage the employer's agent to incorporate the supply aggregator (Weldmax) in the contract as an important third party whose performance will determine the projects' outcome, he did not budge.
"If the employer needed six contractors for the houses, what was the rationale for one supplier? Is there anything in the construction world like anyone supplying everything? The norm is just the supply of major materials.
"Having appointed the contractors and the materials supplier, the terms and conditions of the contract remained the same. In this case, the contractors were requested to provide performance bonds for the entire contract sum when 50 percent to 60 percent of the works is now through a supply model whose guarantees and quality assurances are not in the contract," said the source.
Apparently, the concerns that were earlier raised by the contractors are now causing anxieties among stakeholders as the project is believed to be lagging behind schedule.
About 200 of the 800 housing units that constitute the housing project are expected to be constructed by the end of the year, with the remainder being completed next year.
It is believed that actual progress is at 4 percent while programmed progress should be 7 percent due to "poor material flow".
By now 20 houses should have ground floor slabs cast and super-structure brickwork commencing, but to date five structures have sub-structure brickwork complete.
Added the source: "All the materials that are being issued are not being accompanied by materials certificates. Concrete aggregates were tested and deemed of poor quality. Termite proofing was withdrawn after termites emerged despite earlier reservations.
"Generally, there are lack of guarantees for quality of materials delivered. An example is the notification by the project manager to use bricks whose quality cannot be guaranteed. The contractors' reputation is now at stake in case of failure."
Perhaps the most damning allegations that have been levelled against Weldmax and believed to be forwarded to Amplats include the supply of steel and termite proofing brought without materials handling data sheets and the failure to deploy the scarce materials on site.
As a result of the challenges besetting the project, an instruction to stop use of termite poison was issued on August 9, 2013. Back-filling was stopped and subsequent activities put on hold. Also, there was a supervisor's instruction to stop using bricks issued on August 5, 2013, which, however, was reversed on August 9.
Further investigations established that the attrition between the local project manager, a Mr Qedi Ndaba, and Amplats senior project manager Mr Christian Muvingi over the problems consequently led to the jettisoning of the former by the latter.
Frantic efforts to get a comment from Weldmax director Mr Matsa, who is based in South Africa, were unsuccessful by the time of going to press.
Amplats media and external relations manager Mpumi Sithole had not responded to inquiries sent to him a fortnight ago by The Sunday Mail Business by the time of going to press.
But Unki Platinum Mine general manager Mr Walter Nemasase noted in a recent interview that investigations on the tenders were indeed under way.
"Yes, I can confirm that there are investigations that are taking place over the nature of the contracts that were signed with contractors and how they were executed. I can also confirm that they centre on the housing project that we are presently undertaking," said Mr Nemasase, adding:
"I cannot, however, comment further as the matter is still under investigation."
In addition, the investigations extend to a "suspicious" deal between the miner's agent and a company roped in to supply materials.
Unki management has since confirmed the probe.
It is believed that the Johannesburg Stock Exchange-listed concern is worried that there might be a serious breach in the way the contracts with local contractors were negotiated, a development that might ultimately dent the construction project and inflate the aggregate cost of the venture.
Investigations by this paper show that on October 9 last year Unki Platinum Mine, which is based in Shurugwi, invited companies to tender for the construction of about 800 housing units valued at more than US$66 million.
Six contractors - Dohne, Citizen, Bambanani JV, Newbase Construction, Ubuntu JV and Selbridge - were subsequently awarded tenders.
The tenders were submitted for a supply-and-fix contract where contractors would be entitled to mark-ups on labour, plant and material costs.
Also, contracts entered into were in the form of the NEC3 contract, which is deliberately written to formalise the requirement to carry out good practice project management systems that should assist the project teams in understanding the status of both time and cost for the life cycle of the project.
However, in January this year the employer's agent, Amplats senior projects manager Mr Christian Muvingi, who is based in South Africa, introduced the materials aggregator model where virtually all the materials were going to be supplied by one company - Weldmax - that is also owned by a South African-based businessman, Mr Solomon Matsa.
Sources say the deal clinched by Weldmax, worth over US$26 million, raised eyebrows, particularly the unclear circumstances in which the company landed the award, and the rationale by the project manager to engage one supplier to source all the materials where six local contractors had been engaged.
But what has become more worrying for the stakeholders, including the contractors is the fact that the basic materials that have been supplied thus far, such as bricks, cement and termite poison, could not be supplied timely, while "some of the few materials supplied could not conform to the quality specifications captured in the contract".
And it is further alleged that when contractors tried to engage the employer's agent to incorporate the supply aggregator (Weldmax) in the contract as an important third party whose performance will determine the projects' outcome, he did not budge.
"If the employer needed six contractors for the houses, what was the rationale for one supplier? Is there anything in the construction world like anyone supplying everything? The norm is just the supply of major materials.
Apparently, the concerns that were earlier raised by the contractors are now causing anxieties among stakeholders as the project is believed to be lagging behind schedule.
About 200 of the 800 housing units that constitute the housing project are expected to be constructed by the end of the year, with the remainder being completed next year.
It is believed that actual progress is at 4 percent while programmed progress should be 7 percent due to "poor material flow".
By now 20 houses should have ground floor slabs cast and super-structure brickwork commencing, but to date five structures have sub-structure brickwork complete.
Added the source: "All the materials that are being issued are not being accompanied by materials certificates. Concrete aggregates were tested and deemed of poor quality. Termite proofing was withdrawn after termites emerged despite earlier reservations.
"Generally, there are lack of guarantees for quality of materials delivered. An example is the notification by the project manager to use bricks whose quality cannot be guaranteed. The contractors' reputation is now at stake in case of failure."
Perhaps the most damning allegations that have been levelled against Weldmax and believed to be forwarded to Amplats include the supply of steel and termite proofing brought without materials handling data sheets and the failure to deploy the scarce materials on site.
As a result of the challenges besetting the project, an instruction to stop use of termite poison was issued on August 9, 2013. Back-filling was stopped and subsequent activities put on hold. Also, there was a supervisor's instruction to stop using bricks issued on August 5, 2013, which, however, was reversed on August 9.
Further investigations established that the attrition between the local project manager, a Mr Qedi Ndaba, and Amplats senior project manager Mr Christian Muvingi over the problems consequently led to the jettisoning of the former by the latter.
Frantic efforts to get a comment from Weldmax director Mr Matsa, who is based in South Africa, were unsuccessful by the time of going to press.
Amplats media and external relations manager Mpumi Sithole had not responded to inquiries sent to him a fortnight ago by The Sunday Mail Business by the time of going to press.
But Unki Platinum Mine general manager Mr Walter Nemasase noted in a recent interview that investigations on the tenders were indeed under way.
"Yes, I can confirm that there are investigations that are taking place over the nature of the contracts that were signed with contractors and how they were executed. I can also confirm that they centre on the housing project that we are presently undertaking," said Mr Nemasase, adding:
"I cannot, however, comment further as the matter is still under investigation."
Source - Sunday News